在现代化工生产中,
反应釜温度控制系统扮演着至关重要的角色。作为化工生产过程的核心设备,反应釜的温度控制精度直接影响着产品质量、生产效率和安全性。随着化工生产向精细化、智能化方向发展,温度控制已从简单的工艺参数上升为决定企业核心竞争力的关键因素。
一、温度控制与产品质量的密切关系
化学反应过程对温度具有高度敏感性,微小的温度波动都可能导致反应路径的改变。在精细化工领域,反应温度偏差1℃就可能使产品纯度下降2-3%,直接影响产品等级和市场价值。以医药中间体生产为例,温度控制精度需达到±0.5℃以内,才能确保产品符合GMP标准。
温度波动会导致分子结构改变、副反应增加、晶体形态异常等问题。在聚合物生产中,温度波动5℃会使分子量分布变宽,产品力学性能显著下降。因此,精确的温度控制是保证产品一致性和稳定性的关键。
现代温度控制系统采用PID算法、模糊控制等先进技术,配合高精度传感器,可将温度控制精度提升至±0.1℃。这种精确控制确保了产品质量的稳定性,为企业赢得市场竞争优势。
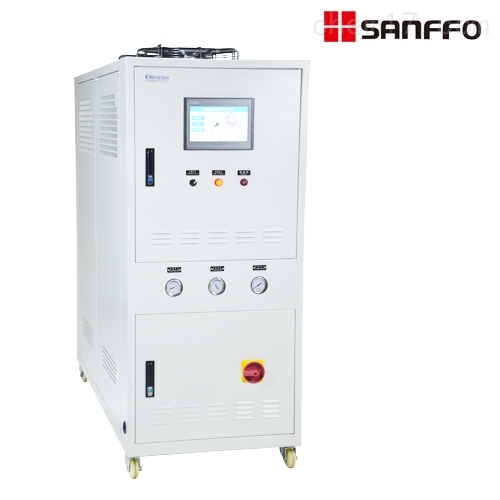
二、温度控制对生产安全的重要保障
化工生产中,温度失控是引发安全事故的主要原因之一。据统计,超过60%的化工事故与温度异常有关。温度过高可能引发物料分解、压力骤升,导致爆炸事故;温度过低则可能造成反应停滞、物料积聚,存在潜在风险。
现代温度控制系统集成了多重安全保护机制。实时监测、自动报警、联锁停机等功能,有效预防温度异常引发的安全事故。例如,在聚合反应中,系统可实时监测反应热,自动调节冷却量,防止反应失控。
先进的控制系统采用冗余设计,配备独立的安全仪表系统(SIS),确保在主控制系统失效时仍能保障安全。这种设计大大降低了事故发生的可能性,为化工生产筑起安全防线。
三、温度控制系统的智能化发展趋势
随着工业4.0技术的应用,温度控制系统正向智能化方向发展。基于大数据分析的预测控制、人工智能算法等新技术,使温度控制更加精准和可靠。系统可自主学习工艺特性,优化控制参数,实现更精细的温度调节。
智能化控制系统可实现远程监控、故障诊断、能效优化等功能。通过物联网技术,多个反应釜的温度数据可集中管理,实现生产过程的全局优化。这不仅提高了生产效率,还降低了能耗,推动化工生产向绿色、低碳方向发展。
展望未来,随着新材料、新技术的应用,反应釜温度控制系统将向更高精度、更快响应、更强可靠性方向发展。这将为化工生产带来革命性变革,推动整个行业向更高质量、更安全、更高效的方向迈进。